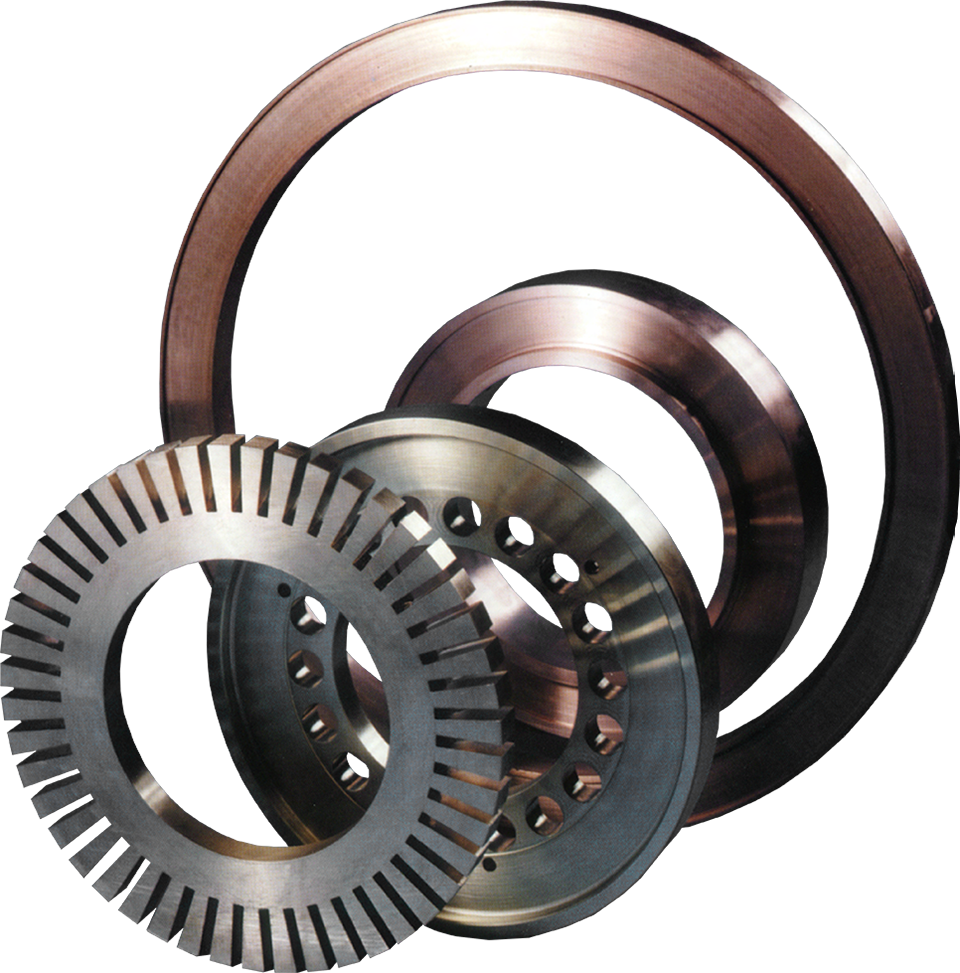
Copper & Bronze Centrifugal Casting Electric Materials
Centrifugal castings are an obvious fit for industrial roll bodies because they are formed round, concentric, and free from mid-wall voids. And, they can be further enhanced by surface machining without compromising the integrity of the metal.
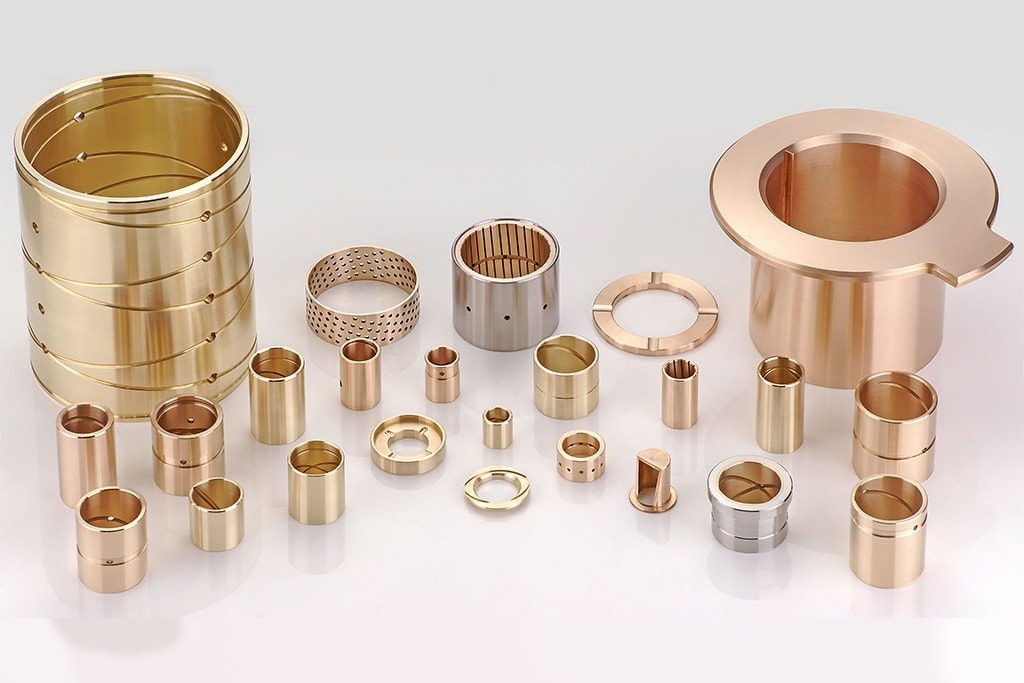
Our Product Centrifugal Bronze Casting
Centrifugal casting is a manufacturing process used to create cylindrical components with a central axis of rotation. This technique involves rotating a mold around a central axis at speeds typically ranging from 300 to 3000 rpm while pouring molten material into the mold.

Spuncast Capabilities Centrifugal Casting Products
D.W. Clark specializes in engineered sand and centrifugal castings with challenging requirements. From simple designs to complex shapes, we're proud to support critical applications across many industries serving infrastructure and defense. The D.W. Clark approach is to engineer every casting project from the ground, up—whether the casting.
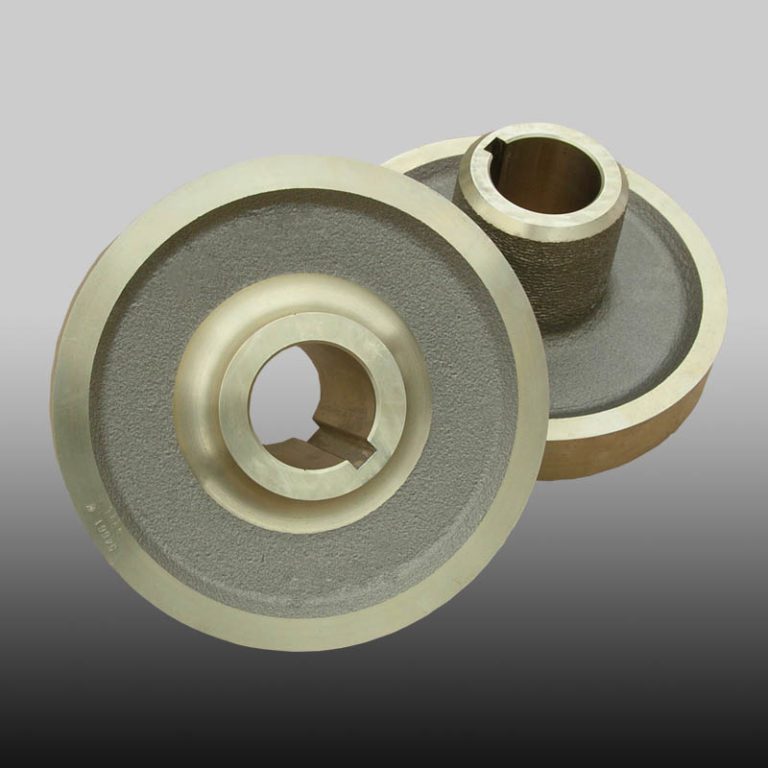
Centrifugal Casting Applications MetalTek
Quaker City Castings can produce centrifugal castings up to 13″ outside diameter in all the materials we pour in our sand-casting operations, including gray iron and ductile iron, steel, stainless steel, carbon steel, heat-resistant steel, and superalloys. Some of the finished parts we produce include cylinder liners, lapping pots, various.

Centrifugal Casting Machine for Large Hydro Guide Bearings—Spins 300rpm up to 127" diameter
Centrifugal casting or rotocasting is a casting technique that is typically used to cast thin-walled cylinders. It is typically used to cast materials such as metals, glass, and concrete. A high quality is attainable by control of metallurgy and crystal structure.
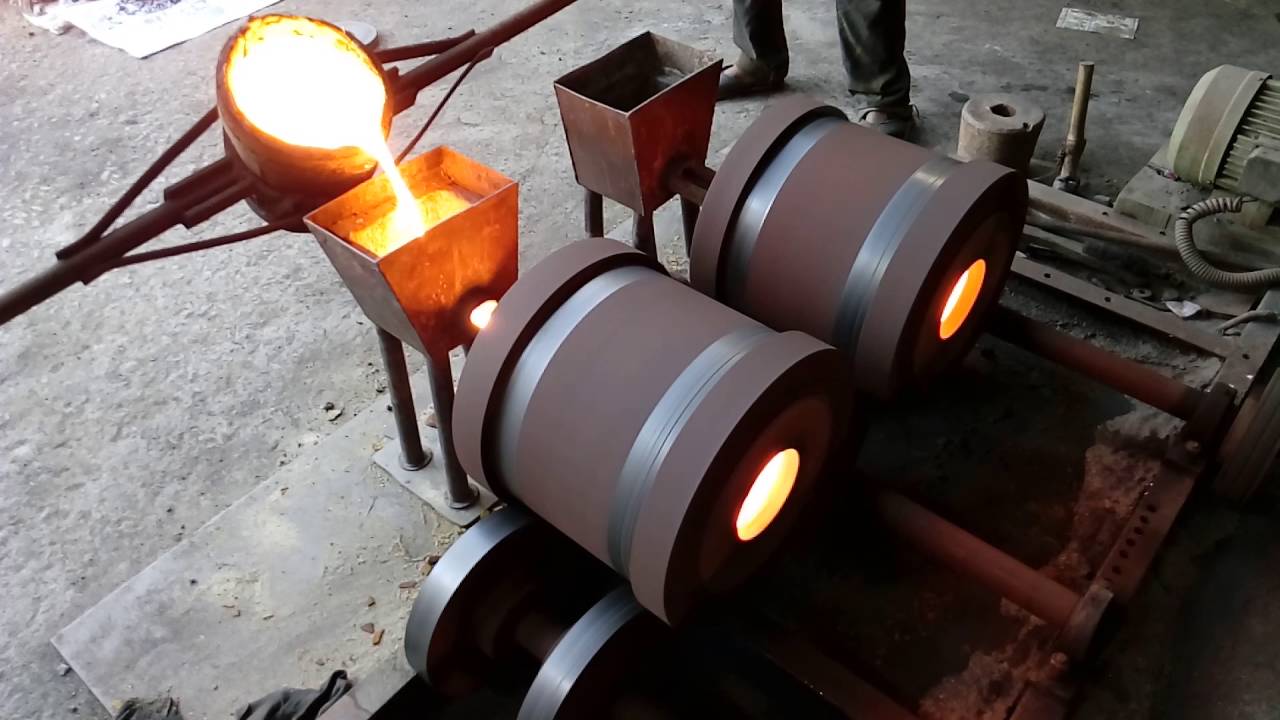
CENTRIFUGAL CASTING MANUFACTURING PROCESS YouTube
Centrifugal casting has a wide range of applications in the industry and is used to make parts such as bushings, engine cylinder liners, rings, brake drums, water supply lines, sewage pipes, street lamp posts and gas pipes.
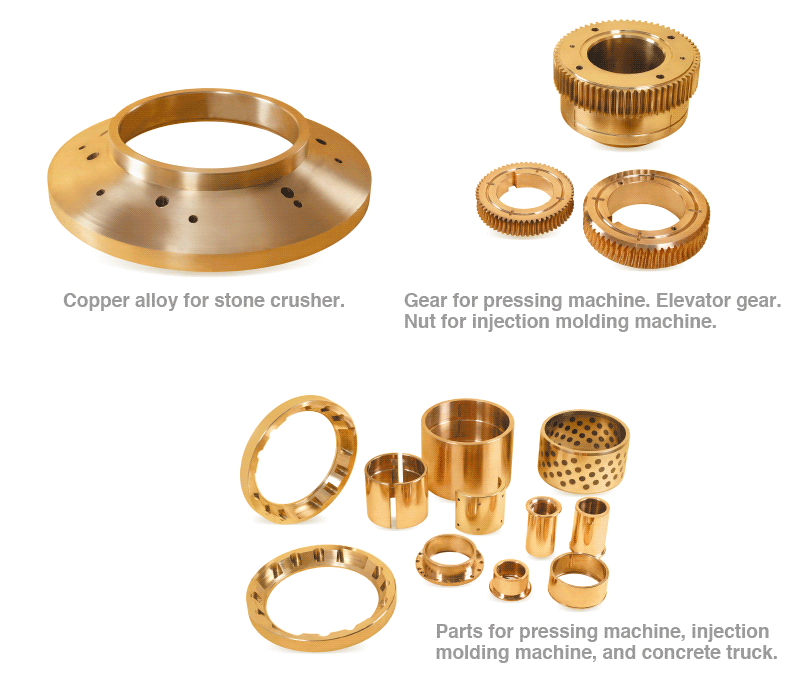
Centrifugal Casting Product
1. Expertise in Many Different Materials We propose ideal steel casting materials for applications in industrial equipment operating under extreme conditions. We supply cast products with high resistance to heat, corrosion, and abrasion for various service environments and property requirements.
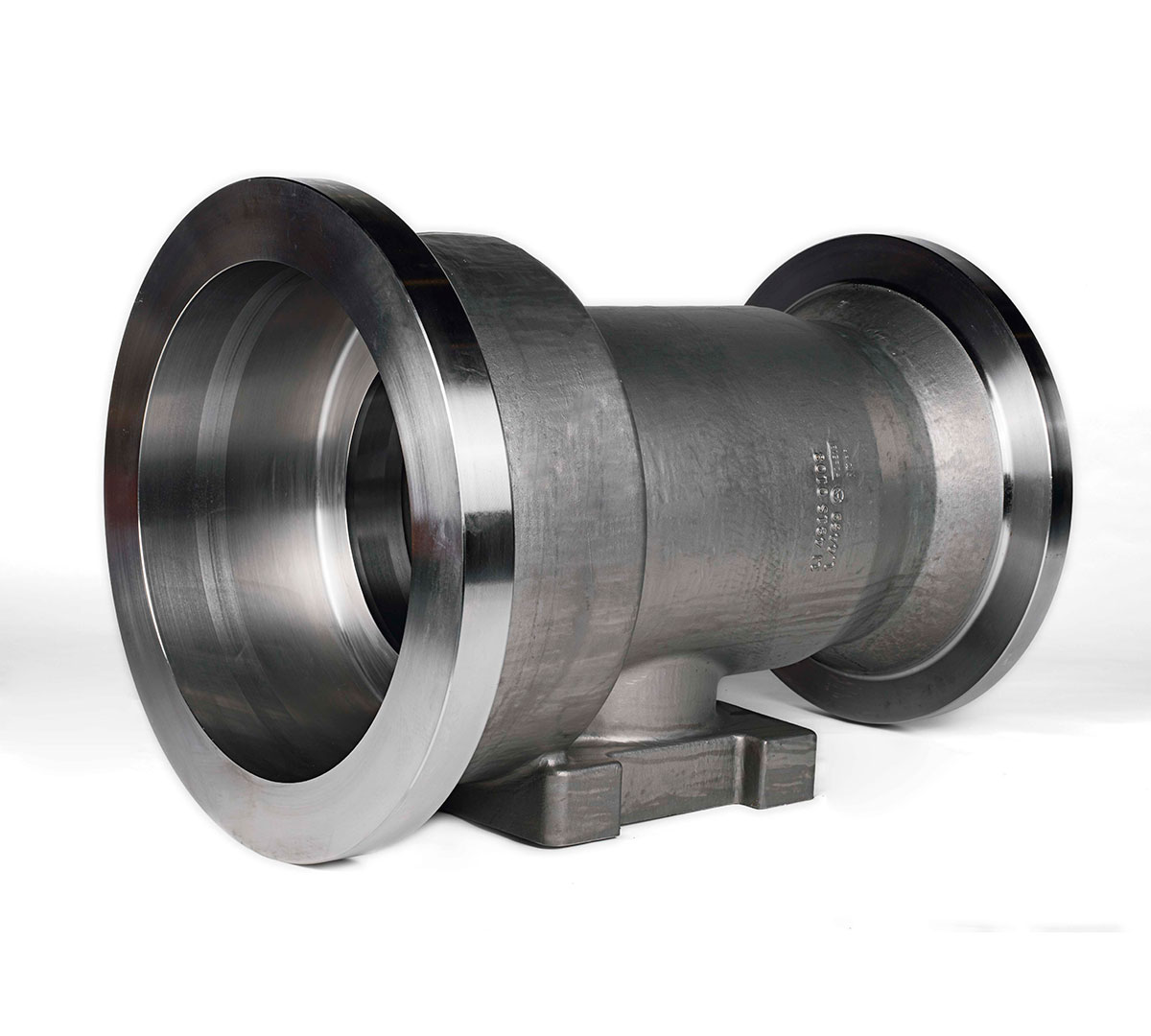
Shaped Centrifugal Casting 1 Ampo
Centrifugal casting is a casting process that is generally used for casting cylinders with thin walls. Learn more at Cast Alloy Products LLC.

Understanding Centrifugal Casting and Its Advantages Bunting Bearings LLC. Powdered Metal
Centrifugal casting produces metal parts with optimum accuracy, superior surface finish, and minimal waste. The process is perfect for manufacturing castings with intricate designs and thin wall sections. There are many advantages to using centrifugal casting for the manufacture of cylindrical and circular parts. They include:

Centrifugal Castings Steel & Alloys Castings Manufacturer
The centrifugal casting method is the method to produce pipes by pouring molten metal into a rapidly spinning cylindrical mold in which centrifugal force from the rotation exerts pressure on the molten metal. In 1952, Kubota developed its first centrifugal casting technology for steel.
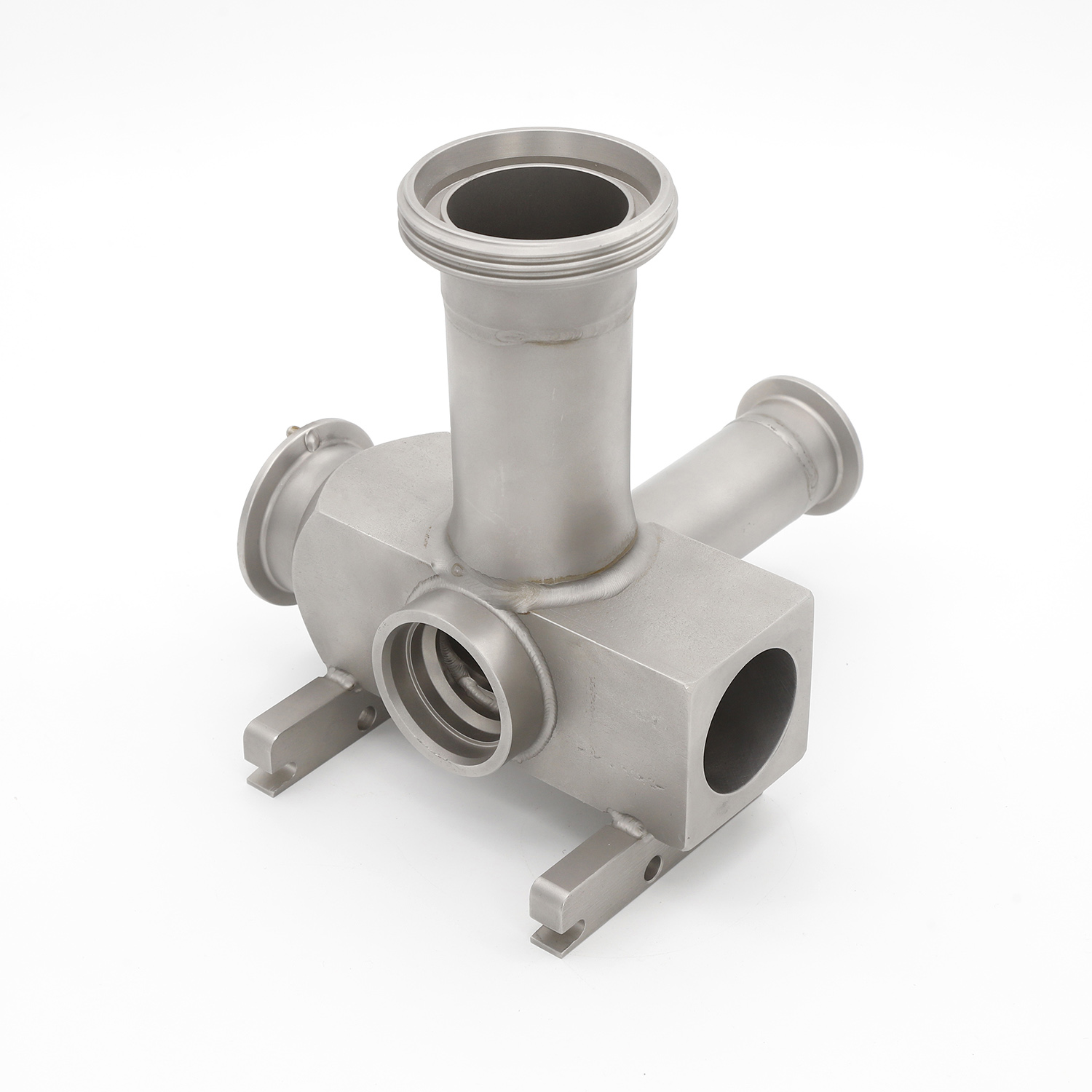
Centrifugal Castings Densen Group Co., Ltd.
Centrifugal casting provides high material soundness and is the metal casting process of choice for jet engine compressor cases, petrochemical furnace tubes, many military and defense components, and other applications requiring high reliability.
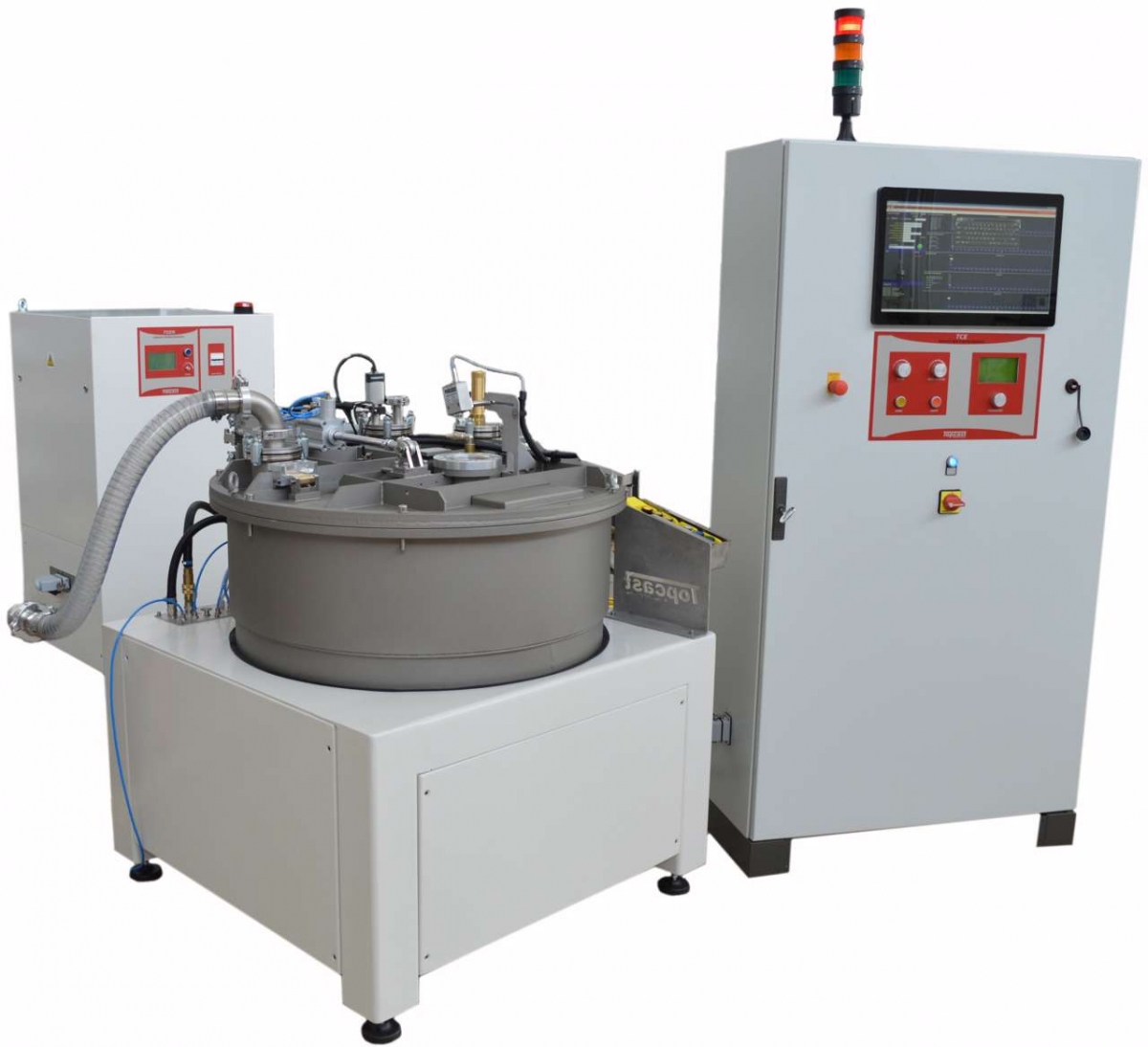
Vacuum Centrifugal Casting Machines in Class A Topcast
Also known as rotocasting, centrifugal casting leverages the power of centrifugal force — the physical force that occurs when an object moves in a curved direction away from its center — to create hollow, cylindrical-shaped objects. From iron and aluminum to stainless steel and even concrete, centrifugal casting supports a wide range of materials.
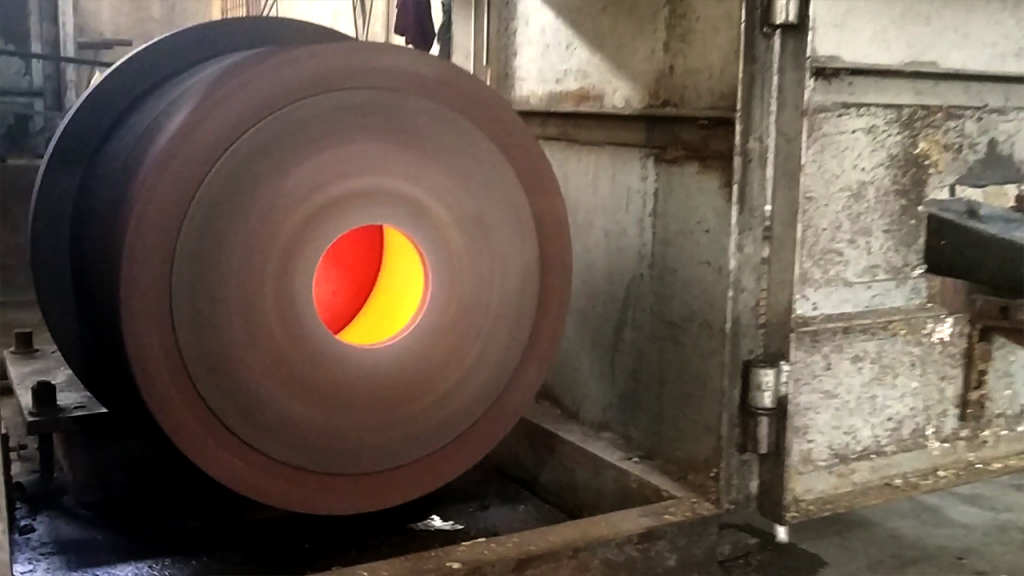
Centrifugal Casting Process Centrifugal Bronze Casting
Spuncast is a full-service centrifugal foundry that manufactures hydraulic cylinders, accumulators, and roll bodies for industries that never quit, like oil and gas, water treatment, glass, consumer goods, and more. Whatever your industry, Spuncast is up for the challenge.
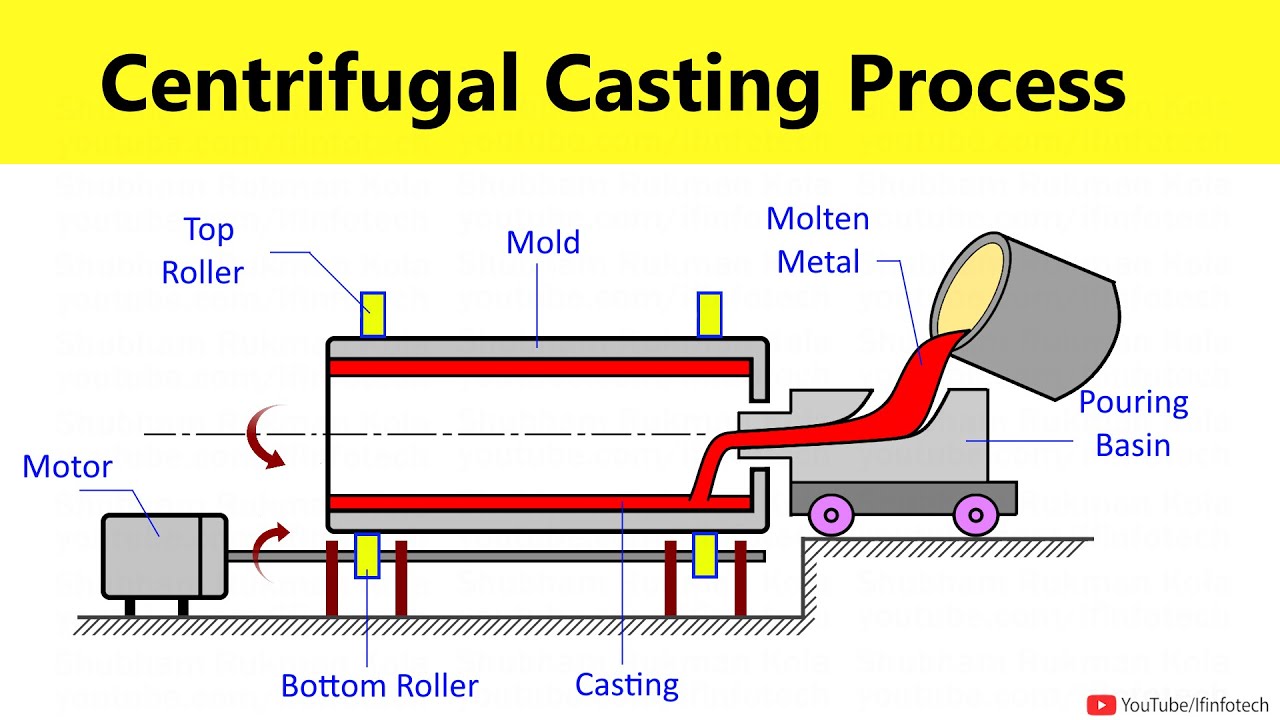
Centrifugal Casting Process Working Animation Manufacturing Processes Lecture By Shubham Kola
Centrifugal casting is a set of casting techniques that ensure top-notch quality of the products and deliver the best overall results. The following text will briefly examine what this casting method is and its advantages for the industry. What Is Centrifugal Casting?
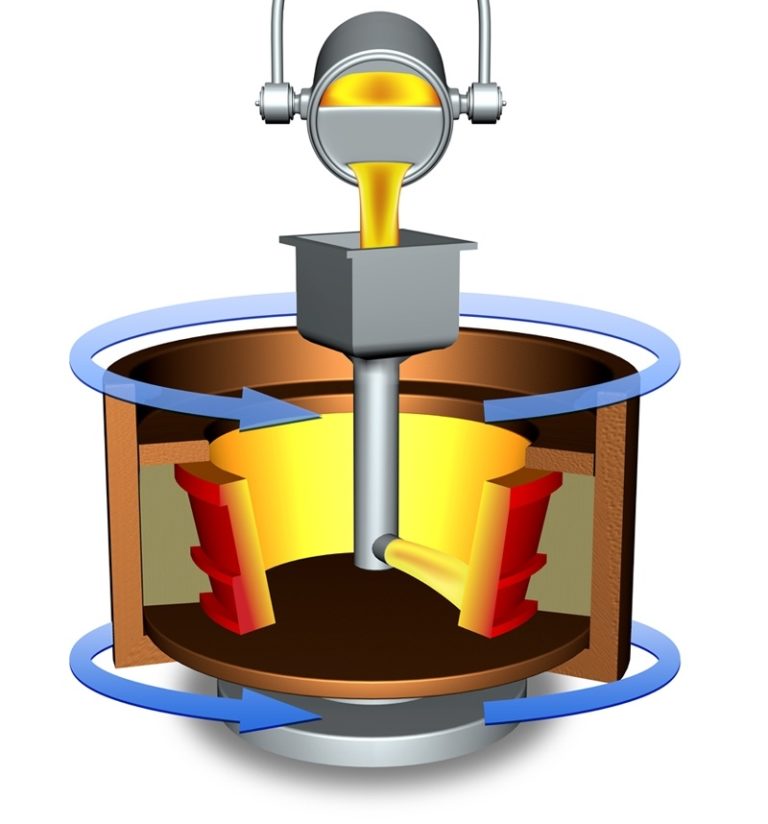
What is Centrifugal Casting and How Does It Work? MetalTek
What is Centrifugal Casting and Why Does It Create Better Tubing Products? Centrifugal casting is a highly efficient manufacturing process for creating hollow cylindrical parts that are economical and offer superior soundness. It's also a process that is often either unknown or misunderstood.
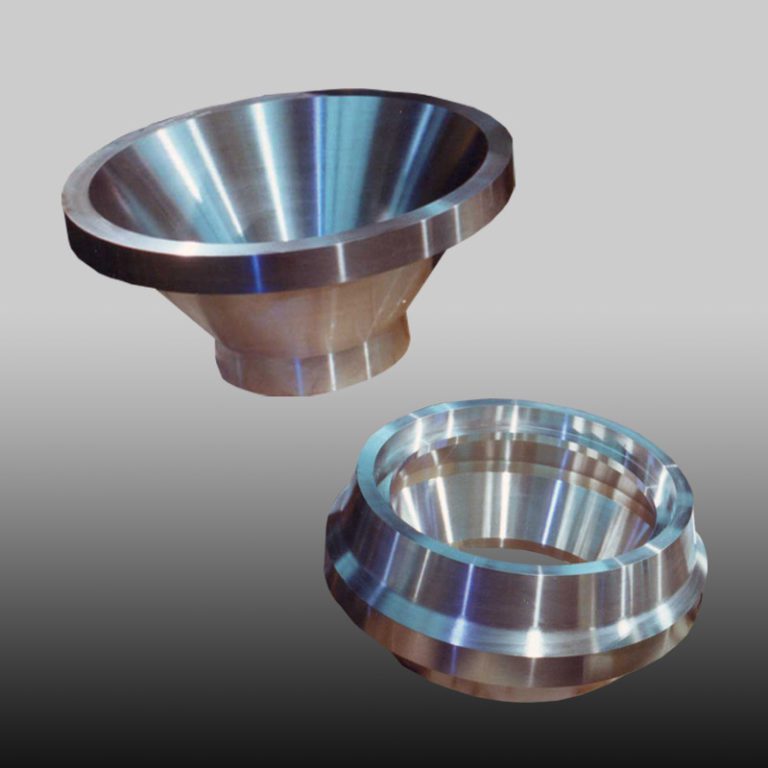
Wisconsin Centrifugal Casting Company MetalTek
Our centrifugal casting technology can produce a variety of weights, lengths, and sizes up to: Weight capabilities of up to 13,000 pounds (5,900 kg) Maximum outside diameters of 44" (1,092.2 mm) Lengths up to 300" (7,620 mm) Material Choices